Micro-Fulfillment Centers (MFC)
StrongPoint provides incredibly effective micro-fulfillment solutions specifically designed for grocery retailers and other sectors as an AutoStore partner. Warehouse and e-commerce may be carried out at very high levels of efficiency by integrating automated order picking with StrongPoint’s best-in-class manual order picking and last mile solutions.
Embedded video
A frozen zone with micro-fulfillment
The first automated frozen zone AutoStore solution in the world is being installed by StrongPoint. This streamlines the selection process and results in significant energy and space savings.
Background in
grocery industry
Our experience in groceries necessitates more intricate integrations with last-mile services and solutions.
Hyper-efficient
The quickest fulfillment option per square foot is AutoStore’s automated picking.
Hyper dense
The solution is perfect for small grocery stores and other merchants with limited space since it makes the best use of available space and has the highest storage density of any automated storage and retrieval system (ASRS).
What is a micro-fulfillment center?
Micro-fulfillment centers (MFCs) are small, frequently partially automated warehouses that can be located in the back of big-box stores or in metropolitan areas. It is often a scaled-down counterpart of large customer fulfillment centers (CFC), which are usually located in rural areas because of space and expense constraints.
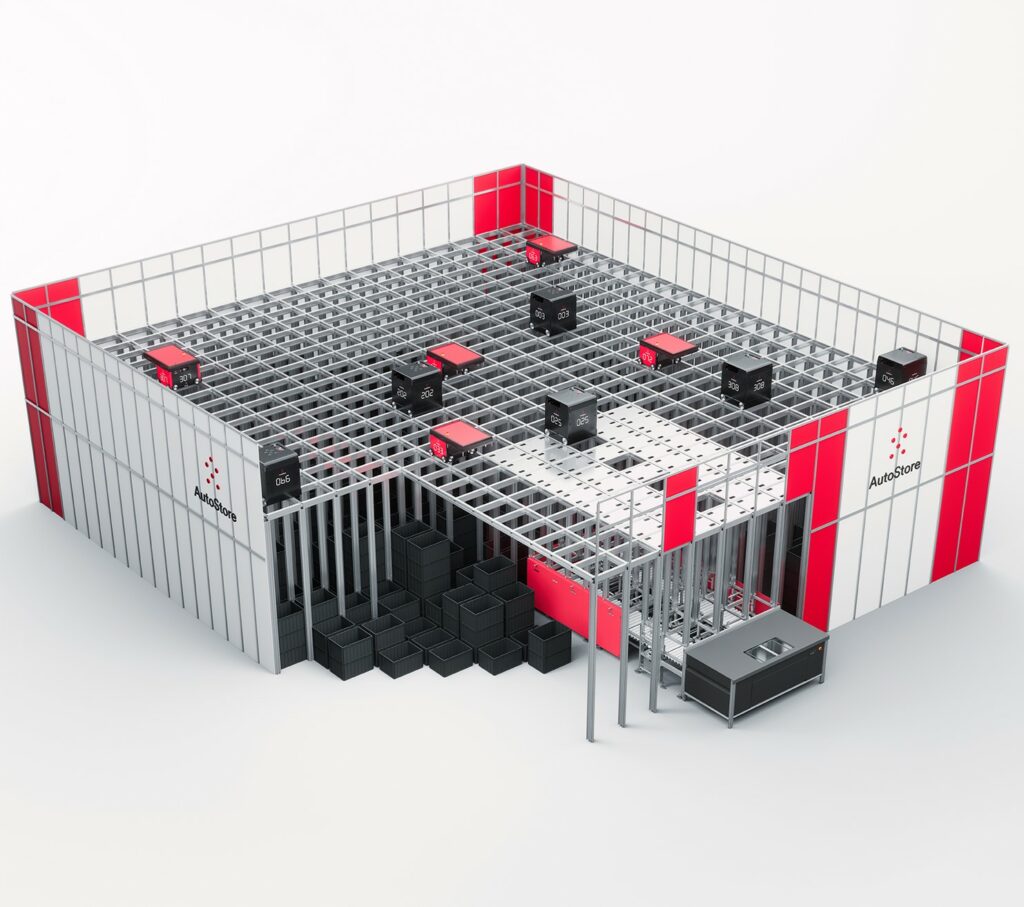
MFC frequently incorporates a system for automated goods-to-worker picking.
The main justification for investing in micro-fuflilment is to increase storage capacity and expedite order delivery, which will save labour costs and expenses related to product storage and order fulfillment.
With the densest automated solution in the world, AutoStore enables any warehouse to make the best use of available space. Items can be picked automatically and very quickly thanks to AutoStore’s cube storage technology, StrongPoint’s software, and setup.
Do you need to add additional things to your warehouse so that they can be picked automatically with amazing efficiency? If so, you should visit an AutoStore micro-fulfillment center that works with StrongPoint. Automation can be applied to almost any kind of e-commerce fulfillment.
We are creating the First Autostore Solution with a frozen food area in the World!
The world’s first autostore solution specifically designed for groceries, with three temperature zones—ambient, chilled, and now frozen, was designed and installed by StrongPoint. This is predicated on AutoStore’s recently developed automated frozen item storage and retrieval system.
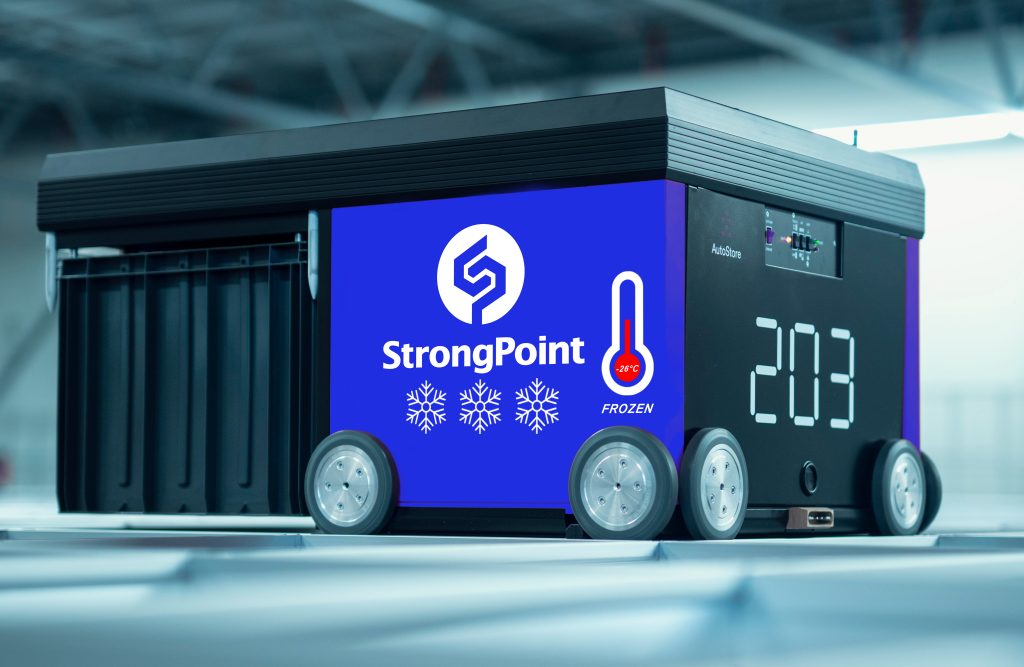
How does it work?
While automating their e-grocery fulfillment services, grocery retailers and wholesalers have frequently relied on manual picking for frozen items.
With AutoStore, grocery stores can now automate in all three temperature zones, increasing productivity and lowering energy costs dramatically. It is anticipated that energy expenses will be lowered by almost 30% in this first installation in history.
Boosting efficiency
Picking efficiency can be further increased by adding more items to the AutoStore grid.
Safer and easier for employees
Employees are no longer required to wear a lot of protective gear when they are in chilly rooms.
Significant energy savings
Energy use will drop by about 30–40% if frozen goods are added to the AutoStore grid instead of being picked by hand.
Want to know more?
To assist with the planning and implementation of a comprehensive automation setup that is integrated with our top-notch last mile solutions, StrongPoint provides complimentary workshops.
The first AutoStore partner with a Grocery Focus
Being the only AutoStore partner that specialises in groceries, StrongPoint is in a unique position to maximise the potential for grocery stores and wholesalers thanks to our industry experience. Our areas of experience include how to set up the warehouse, manage items from various temperature zones, integrate with seamless last mile solutions, and combine manual picking for certain commodities. Throughout the entire procedure, StrongPoint can guarantee operating speed.
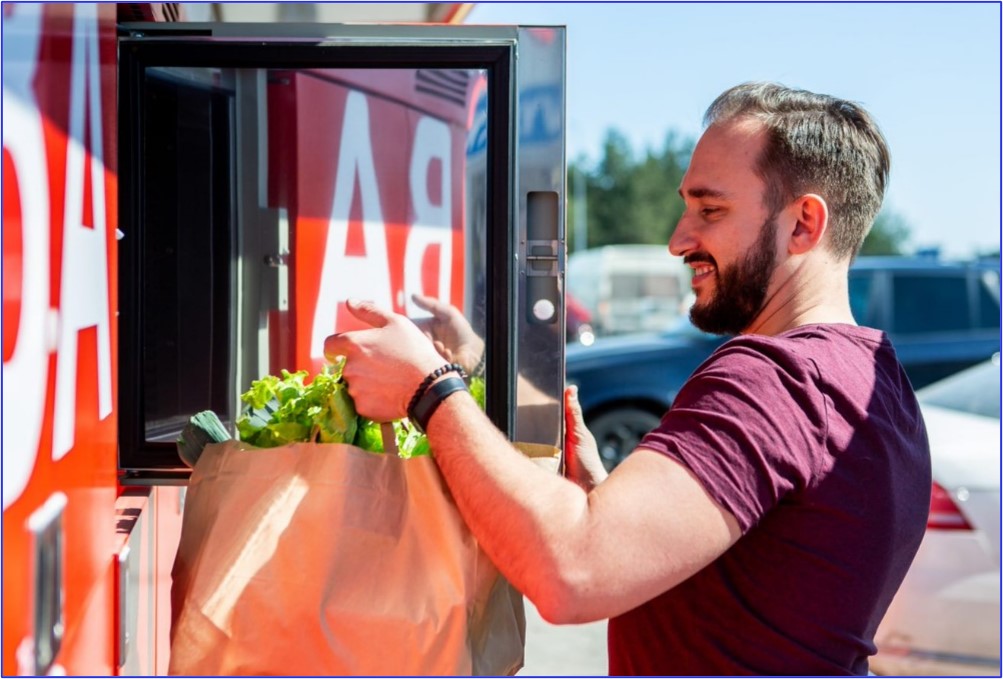
Last mile integration
StrongPoint offers the widest range of last mile solutions on the market, managing both home delivery and all types of click & collect. Do you want to ship goods straight to the consumer from the warehouse? The most effective solutions available on the market can be smoothly integrated by us.
Embedded video
Energy conserving
Very little energy is needed by the robots in the MFC. Actually, one vacuum cleaner uses more energy than ten robots. The secret is clever inventions and eliminating energy-wasting fixtures like lights and heaters. About 30% less energy is used for frozen foods thanks to the newly integrated frozen section.
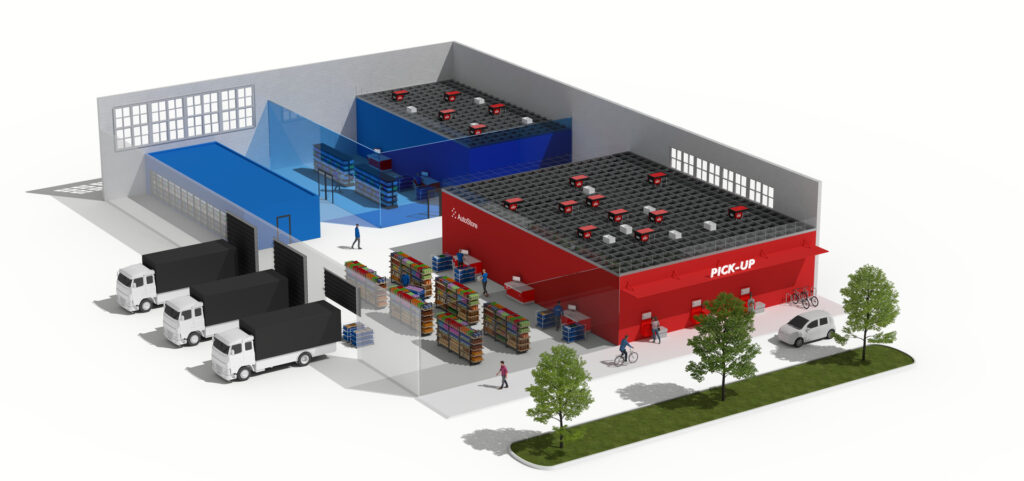
Consultancy regarding drawing the entire storage plan and operation
Take advantage of our experience! We can assist in planning the layout of the storage facility as well as the best locations and methods for carrying out each step of the procedure. What truly sets us apart from the others is our attention to the entire process.
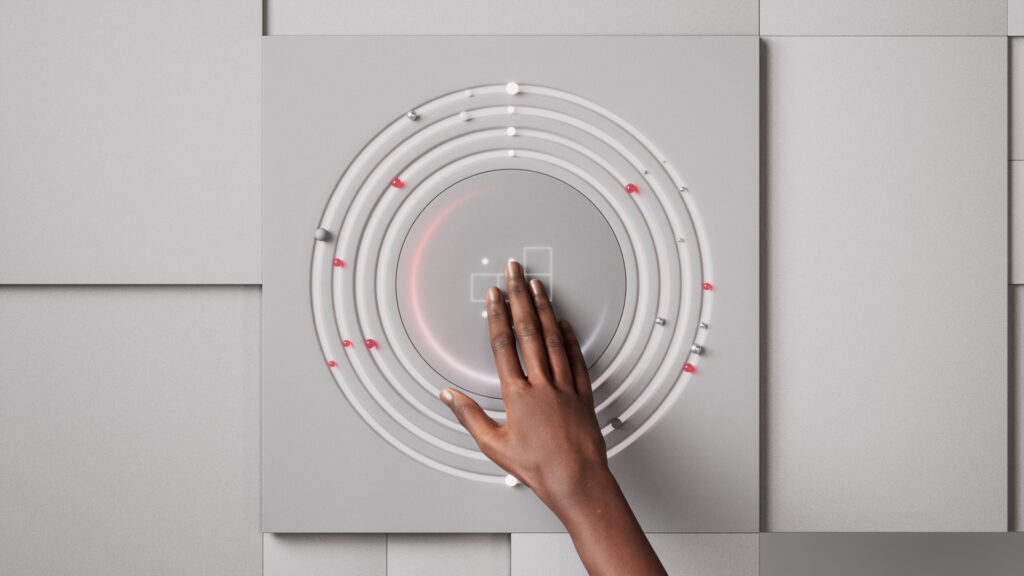
Smooth system integration
Using pre-made APIs, the technology has been integrated with hundreds of warehouse management systems worldwide.
What our customers say
Two efficiency-obsessed Norwegian companies
Both StrongPoint and AutoStore are based in Norway and put up a lot of effort to help our customers become more efficient.

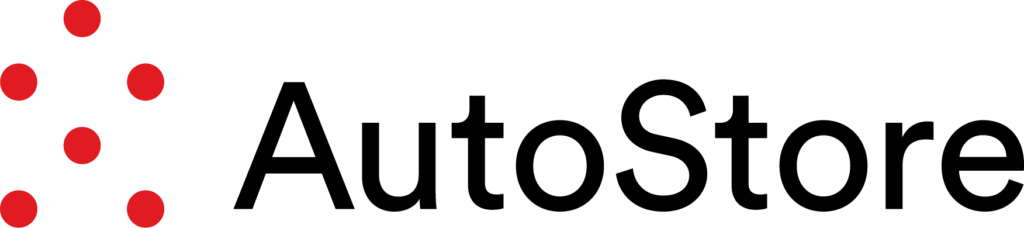
Last-mile integration and non-automated item selection
Beyond automation, StrongPoint’s automation solution can increase an e-grocery solution’s overall efficiency and be customised for e-commerce that isn’t related to food.
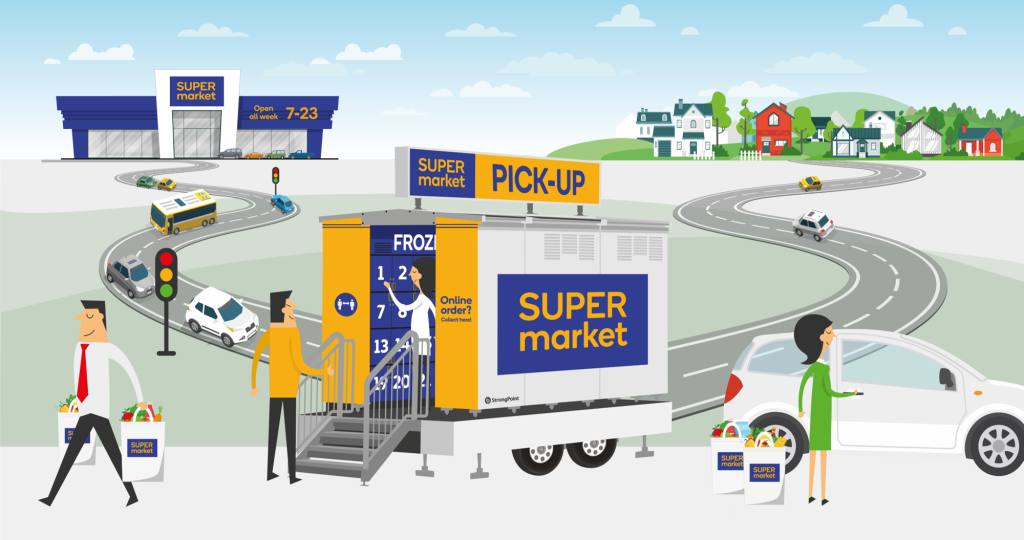
Numerous SKUs in the grocery industry are just not suitable for automation. It makes more sense to pick these manually, especially for large products and fast-movers.
You still have to expedite the process of getting those orders out of the warehouse door. Perishable goods require extremely effective last-mile integration, from click-and-collect to home delivery. Rapid fulfillment is also required for many other e-commerce consumer goods, such as books, clothes, and home goods. There, we’ve got you covered.
StrongPoint offers single-provider access to the most effective manual order-picking systems in the world, as well as completely seamless integration into our many last-mile services, which include home delivery, quick-commerce pickup, and supermarket lockers, and cover a variety of products and types.
Your one-stop shop for all things e-grocery, including last-mile, automated, and manual.
The components that create the magic
A profitable and extremely efficient micro-fulfillment requires a few components. Here is a closer look at each of the individual parts..
The grid
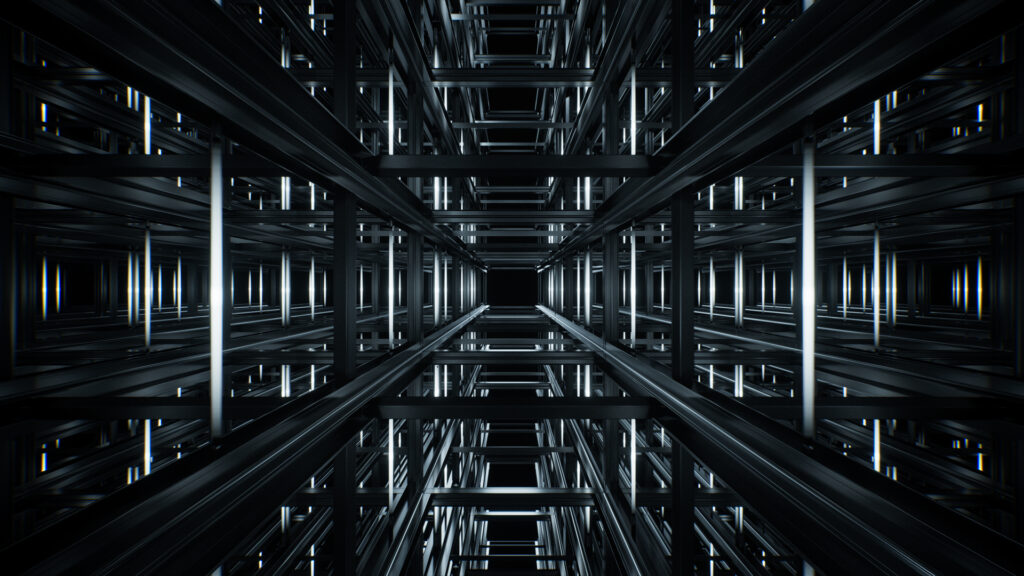
Everything is held together by the aluminum grid. This is the tracks and bin placement infrastructure that the robots use to navigate and locate the appropriate bins containing the appropriate goods. Only the warehouse itself can limit the grid’s size and shape; it can grow in any direction.
The bins
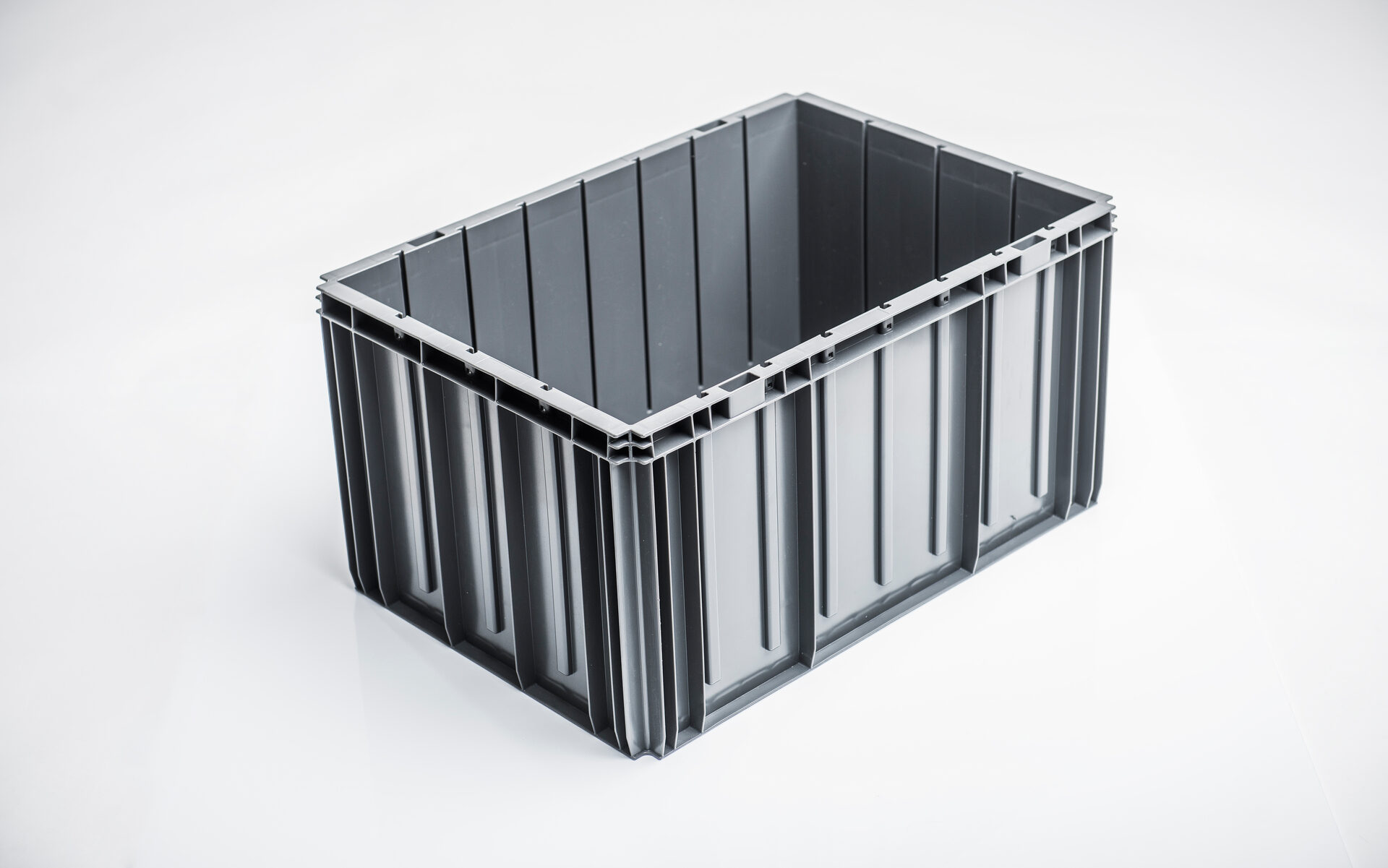
Your products are stored in the bins. Our solution’s bins are robustly constructed from a long-lasting material. They have an incredibly long lifespan when handled gently by robots. Each bin is identified by a unique number that is printed on the bin’s label and kept in a database. You can keep different things in the same bin by dividing it into multiple compartments. The bins come in a variety of materials and heights.
The robots
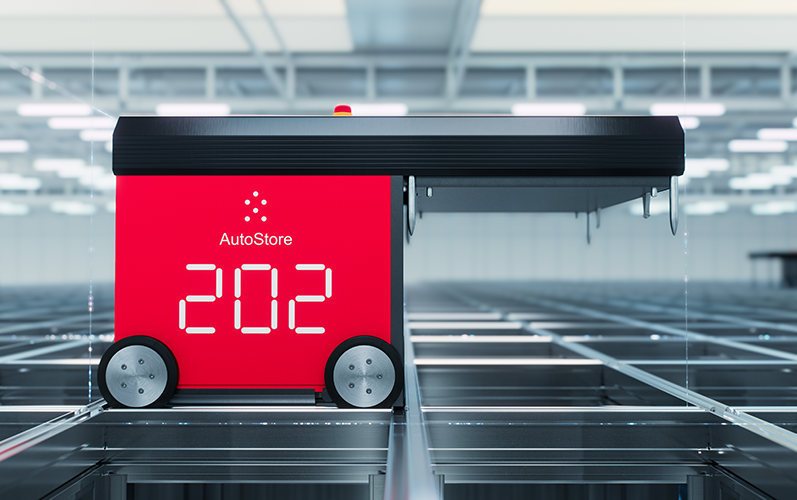
The system’s real employees are the robots. They gather the items you require while racing back and forth along the grid. Every time they brake or lower a bin, they are automatically charged and operate around the clock. In order to prevent overcharging, the robots will automatically charge themselves when more is required. The robots have been working nonstop for more than 15 years, and this leads to a healthy battery. Every second, the robots diagnose themselves and report any discrepancies in their data. If a robot is summoned to the service mezzanine, another robot will take its position automatically.
The manual picking
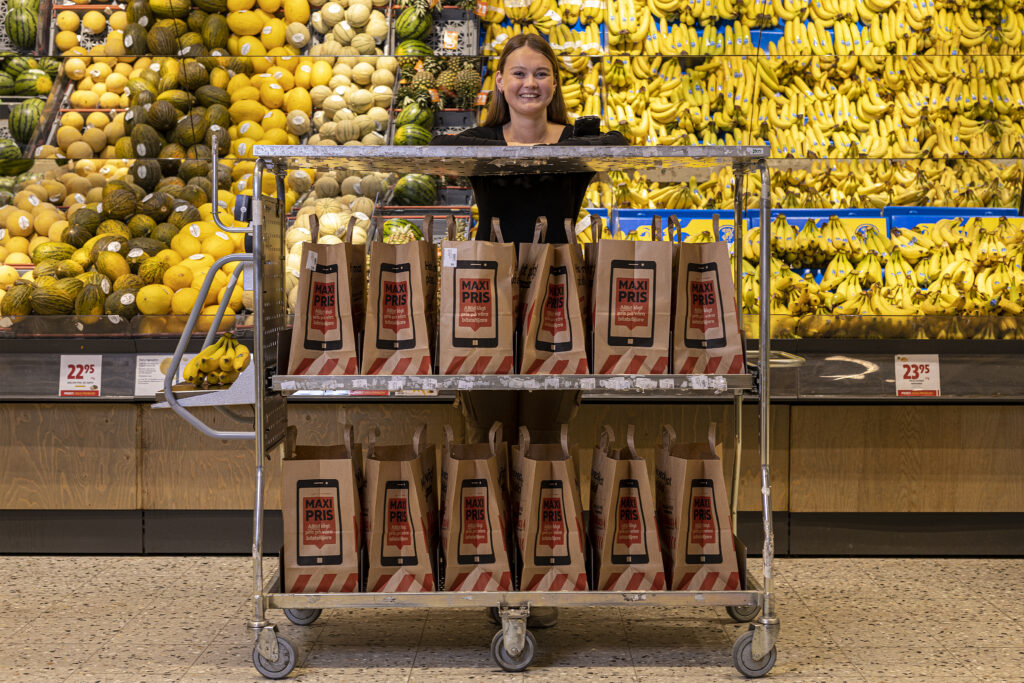
There will inevitably be certain challenges with automating a grocery micro-fulfillment center, such as for products that require manual picking, like big items and some fruits and vegetables. These frequently make up a sizable portion of an internet purchase. Fortunately, StrongPoint’s Order Picking solution, which was developed specifically to increase the effectiveness of manual picking, may be used to optimise this step of the fulfillment process.
The workstations
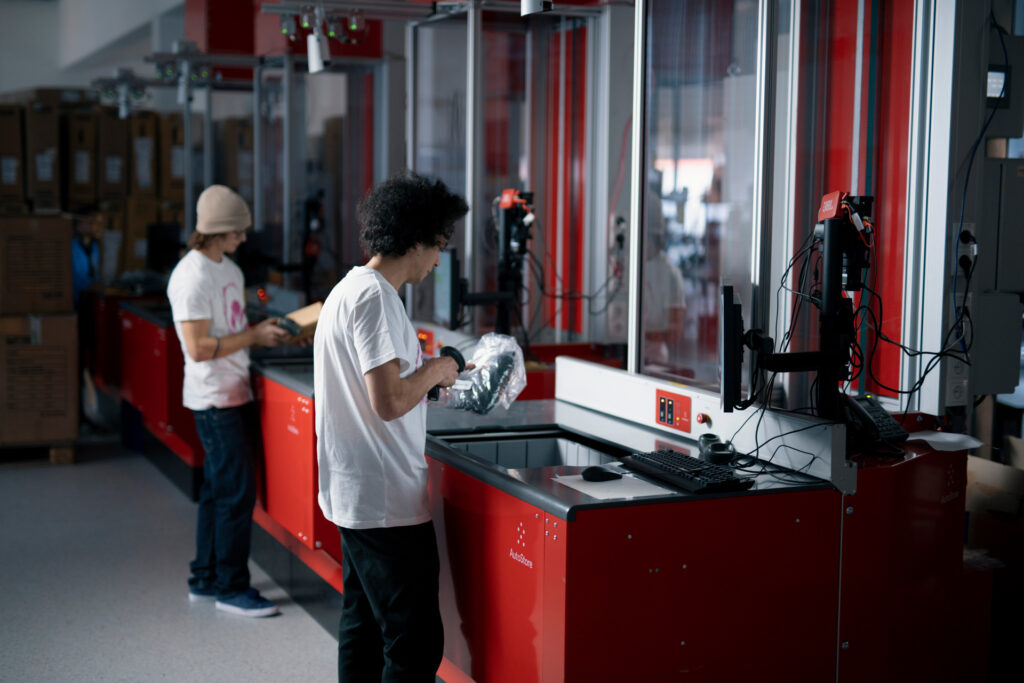
Users receive the items from the MFC at their desks. One straightforward conveyor port, a swing port, a carousel port, or a modular workstation could be the workstation. The workstations are made to be as user-friendly as feasible while maintaining the greatest level of user safety and ergonomic adaptation. Because the movement and technical solution have been refined via millions of tests, smart covering and sensors ensure that your products and employees operate safely. at live installations as well as AutoStore Labs.
The controller
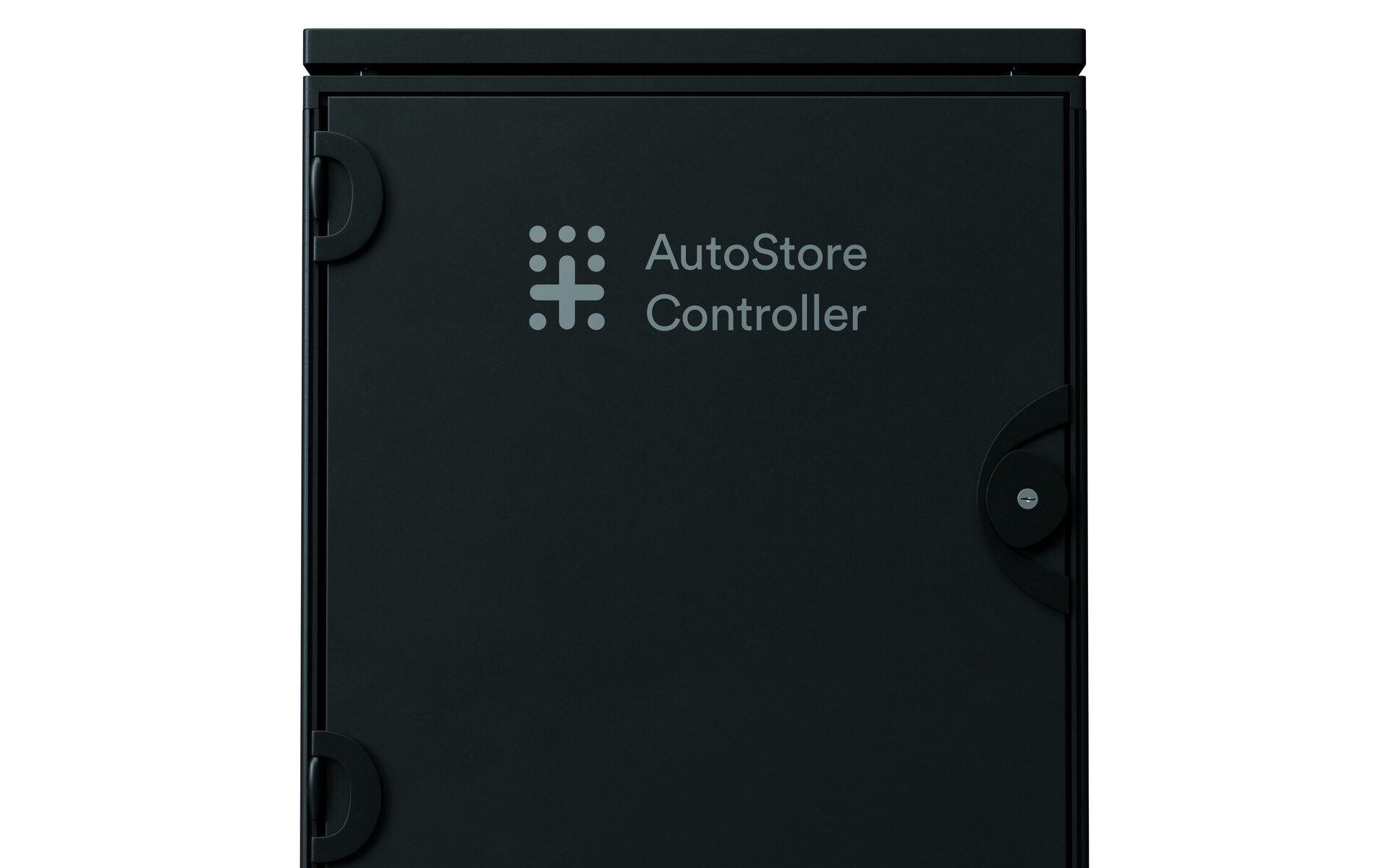
The micro-fulfillment center’s controller serves as its command center. It registers robot and bin positions, prepares and schedules jobs, manages traffic, grants service staff access, and much more. Most significantly, the controller is responsible for controlling the robots’ movements and continuously determining the most efficient way to operate.
Warehouse Management System (WMS)
StrongPoint’s Micro-Fulfillment Centre (MFC) and Customer Fulfillment Centre (CFC) are made possible by Blue Yonder’s leading Warehouse Management System (WMS), whixh may function as a Warehouse Execution System (WES) or as a WMS.
With a long history dating back to RedPrairie and more than 30 years of development, the Blue Yonder Warehouse Management System has become a well-known and extensively used system that has been implemented in more than 40 countries and has more than 1,200 active locations.
It’s a well-established WMS with a long history in automation and groceries. It offers several automation features right out of the box, which we have expanded for our clients’ advantage.
As a Blue Yonder Partner, StrongPoint is able to market, deploy, host, and maintain the Blue Yonder WMS, which we offer to our customers as a software as a service (SaaS) model.
Blue Yonder Dispatcher WMS Supplied as a Service
We supply the Blue Yonder WMS as a managed Service which includes:
- Hosting in public cloud (AWS, Azure or Oracle)
- Proactive maintenance
- 2nd line support
- 3rd line support
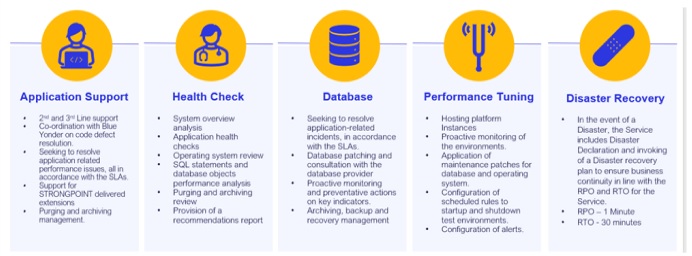
Deep Vertical Capabilities
The quality of WMS systems depends on the customers and verticals to which they have been implemented. Almost every industry, including grocery and e-commerce, has successfully implemented the Blue Yonder WMS. This indicates that it has the breadth and depth of capabilities to handle practically any operational procedure in the most effective manner, enabling you to minimise labour costs and obtain a return on investment.
Highly configurable
Our customers benefit from a system that has been built from the ground up to be user adjustable, thanks to our experience in the 3PL sector, where configurability and ease of use are crucial WMS system pillars. The majority of use cases can be handled by us and our customer’s without resorting to code, which speeds up deployments and lowers the cost of ownership.
Interfaces, functions and policies, and options are all user-configurable components. Language text, Web screens, dashboards, labels, reports, and handheld conversations.
Automation capable
Although many WMS systems have trouble with automation, the Blue Yonder WMS has a long history of automation and contains an Automation module that has all the features and capabilities you would anticipate from a warehouse execution system..
Scalable and referencable
The system’s scalability and resilience have been demonstrated by more than 1200 clients, ranging from the smallest to the biggest Tier 1s.
Integrations, support and analytics
You may now be curious about how this solution relates to your current IT infrastructure and solutions. The systems must communicate with one another, after all. Thankfully, we’ve made it as simple as we can.
Standard APIs for integration
You can link the solution software with your current ERP, e-commerce, or comparable system. StrongPoint’s ready-made APIs are used to do that. For the most seamless functioning possible, we will help you further with anything you require.
Customer support
The IT department doesn’t want to waste time debugging in the infrequent instances when anything goes wrong. StrongPoint offers 24/7 customer service to save you time and avoid needless hassles.
Dashboard and analytics
Naturally, you want to monitor the solution after it has been implemented. The back office is accessible via a web interface, and StrongPoint’s software is hosted on a cloud-based platform. You may view the efficiency, the quantity of orders processed, and other details here.
Contact us today
Interested in our solutions? We’d be happy to connect! Reach out using the form below and we’ll get back to you as soon as possible.
Thank you for getting in touch. We will get back to you as soon as possible.